Retrofit
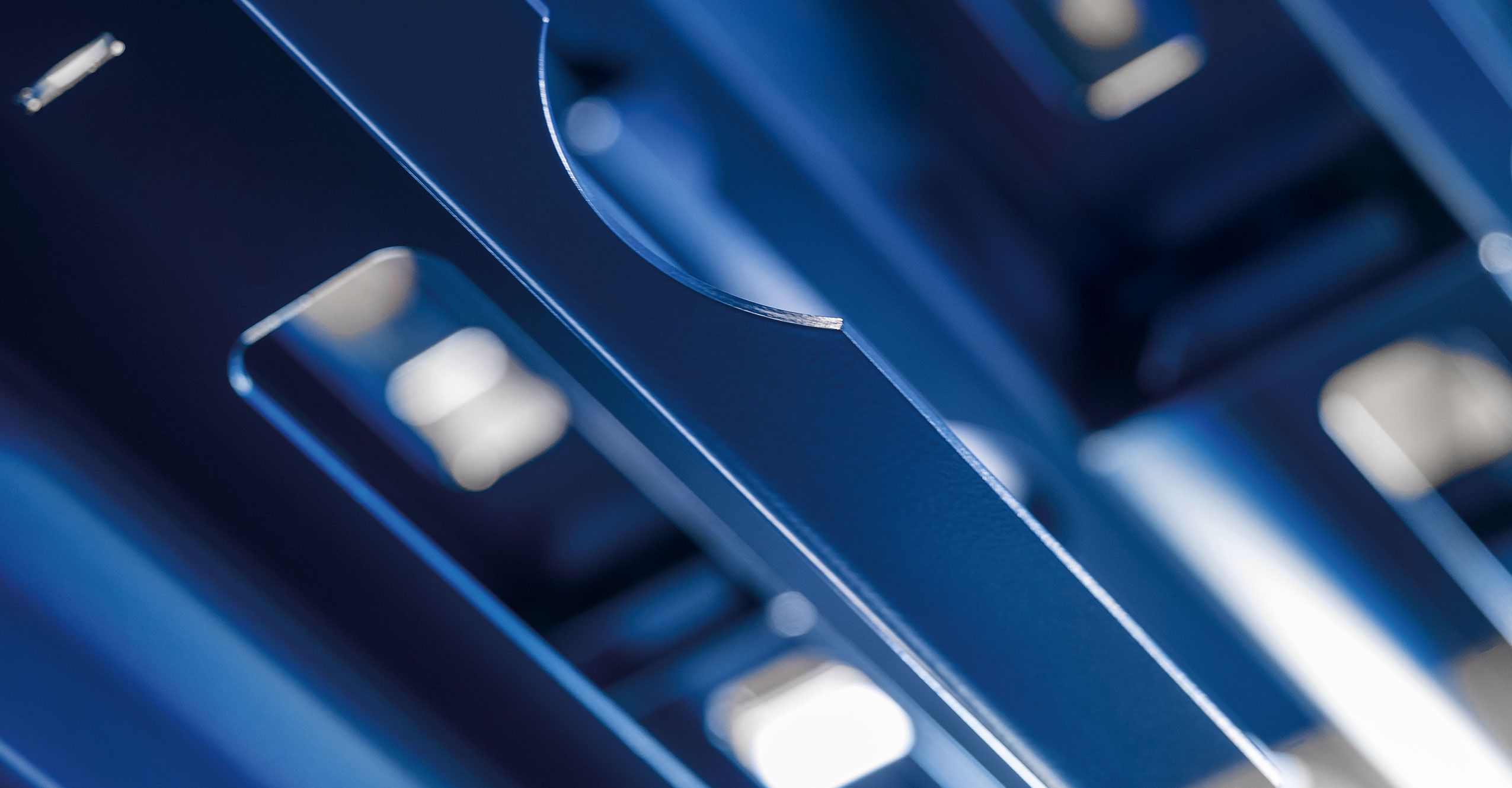
Retrofit
WHY WAIT MONTHS FOR A Replacement WHEN YOU CAN RENEW YOUR STORAGE SYSTEM IN JUST 2-3 WEEKS?
STOPA, one of the leading premium manufacturers of automated storage systems, makes it possible.
Through a RETROFIT, we bring existing storage systems up to the latest technological standards, increasing their efficiency and lifespan. We replace outdated systems and components for which there is no longer support, such as DC motors, ComCon control systems, operating systems like Windows 7 or older, and much more. We introduce current, technologically advanced components, thereby guaranteeing a quick ROI (Return on Investment).
With timely modernization, you not only avoid unnecessary downtime but also the use of the latest drive technologies offers significant productivity advantages. Our decades of experience and over 2,500 installed systems worldwide guarantee you quality and reliability.
BENEFITS AT A GLANCE
Benefit from increased system and spare part availability, reduce costs, and minimize downtime.
-
Reliable system availability
-
Higher spare part availability
-
Lower maintenance costs
-
Simplified error analysis and service support
-
Reduced downtime
Customer Story
AVOIDANCE OF DOWNTIMES
Retrofit Services
STOPA’s RETROFIT services are as versatile as your challenges. Choose between two different retrofit options:
Option 1
PARTIAL RETROFIT
- Vulnerability analysis and definition of modernization options
- Update of key system components
- Reduction of failure rate by replacing discontinued components with current, innovative technology
- Control technology upgrade by replacing old control components
- Operating hours counter and diagnostic functions
- Logging of messages and transport orders
- Precise system control through permanent status messages
- Provision of standardized RETROFIT kits
- On-site conversion, including commissioning
- 12 months warranty on all new parts
- 10 years spare part availability (5 years for control components)
- Detailed documentation
Option 2
COMPLETE RETROFIT
- Performance optimization and secure protection against system failures through complete renewal
- Replacement of all discontinued components with current, innovative technology
- Update of the central system components such as control, drive technology, safety technology, bus system, and much more
- Operating hours counter and diagnostic functions
- Logging of messages and transport orders
- Precise system control through permanent status messages
- Provision of standardized RETROFIT kits
- On-site conversion, including commissioning
- 12 months warranty on all new parts
- 10 years spare part availability (5 years for control components)
- Detailed documentation
your contact person
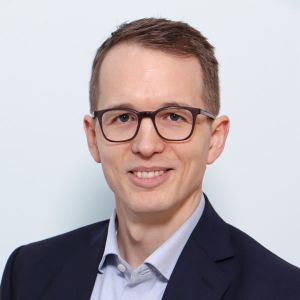
Robert Stockinger
After Sales Manager RETROFIT
STOPA Anlagenbau GmbH
Industriestr. 12
77855 Achern-Gamshurst
Tel +49 7841 704-441
Fax +49 7841 704-190
retrofit@stopa.com
ENQUIRY
Contact
STOPA Anlagenbau GmbH
Industriestraße 12
77855 Achern-Gamhurst