Investing in productivity
By using an automatic STOPA COMPACT sheet metal storage system, CNH Industrial Belgium N.V. has sustainably increased the productivity of its connected laser cutting systems and thus of its entire sheet metal processing. However, the operator is already thinking ahead: he wants to almost triple the length of the system from the current 45 meters and connect all of his laser cutting systems.
The agricultural machinery manufacturer, which operates under the New Holland brand, says that it needs additional capacity for sheet metal processing at its center of excellence in Zedelgem, Belgium. With this in mind, it has invested in the STOPA COMPACT and four laser cutting machines, replacing two old machines with the new ones.
Koen Mergaert, who is responsible for work preparation, sheet metal processing and turning at CNH Industrial Belgium, stops in front of the storage system supplied by STOPA Anlagenbau GmbH, Achern-Gamshurst, during his tour. “Previously, we supplied all the machines with the help of a bridge crane. While it took half an hour to change a sheet metal package on a laser cutting machine using the crane, it now takes only two minutes in automatic operation. In addition, we can work around the clock in the area of automation, largely without the need for human intervention. We also take advantage of this option on Saturdays and Sundays, for more than twelve hours each day.”
Johan Vermote, work preparation sheet metal processing, adds: “Furthermore, we can manage with fewer people when we load the new machines. This is primarily due to the fact that we supply the four machines connected to the storage system with sheets without having to use the crane. For the non-connected machines, we still need two crane operators per shift. In addition, one operator is needed for two of these machines. If this operator takes a break or is busy elsewhere, additional waiting times could occur at the machines in question.”
More efficiency
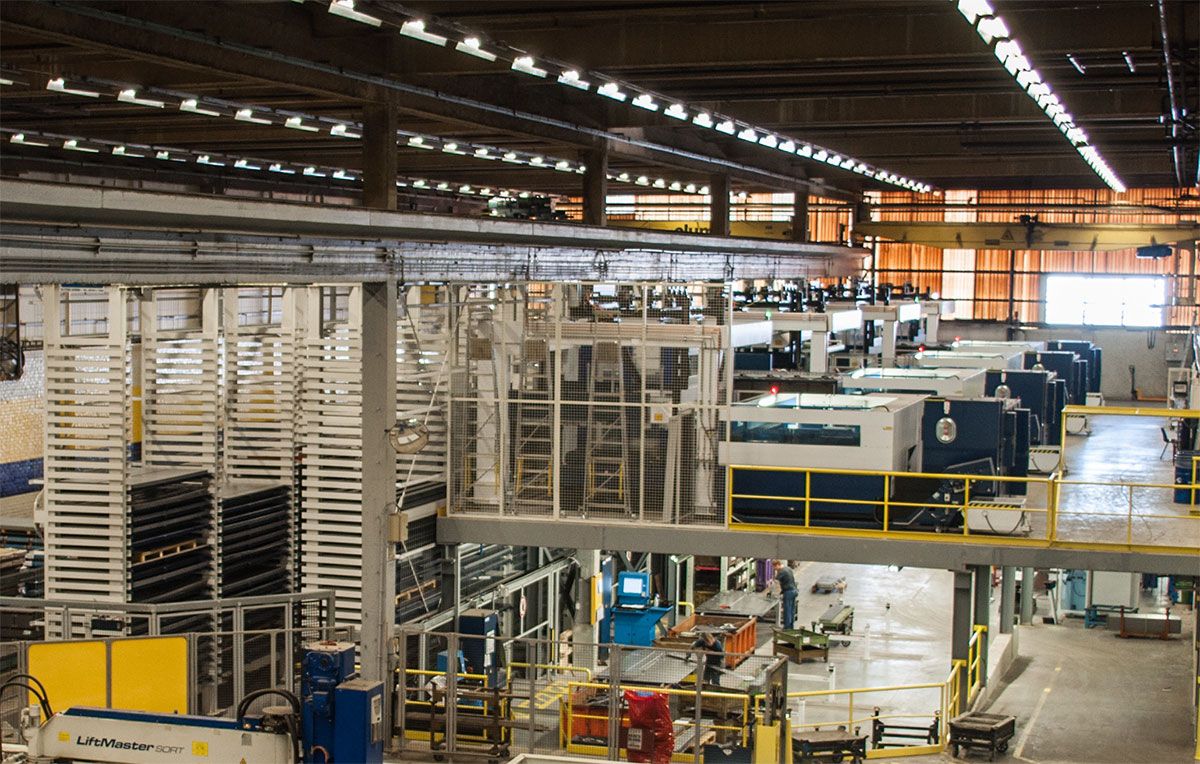
By using an automatic STOPA COMPACT sheet metal storage system, CNH Industrial Belgium has sustainably increased the productivity of its entire sheet metal processing.
Previously, the agricultural machinery manufacturer, which produces 14 combine harvesters a day, and 17 in the peak season, stored the sheets on the floor. This often meant that the crane had to be used to restack the sheet packages in order to pick up the desired material. On top of that, the crane was also used to return unprocessed sheets to storage. This is still a task that has to be performed for the machines that are not connected to the system. In addition, crane trips with a load also pose a safety risk, especially as they can cover distances of up to 250 meters.
Koen Mergaert leafs through a set of statistics. “Before the automation, we bought in 50,000 processing hours from suppliers every year. Today, we only place orders in the high season and for just 20,000 hours. Because we have expanded our in-house production, the number of transports and logistics costs are also falling.” Due to the higher productivity, the amount of complex components that CNH Industrial Belgium has to buy from suppliers for its sister companies is also decreasing, and these components are often more expensive than they can be passed on.
Johan Vermote points to the statistics. “Since the automated storage system enables us to process more sheet metal and produce a greater variety of parts within a defined period of time, we can pack and utilize the sheets more economically. As a result, the scrap rate has fallen by one percent. Considering that 45 percent of the 20,000 tons of sheet metal we process each year pass through the STOPA COMPACT, that is a lot. And the volume will increase.”
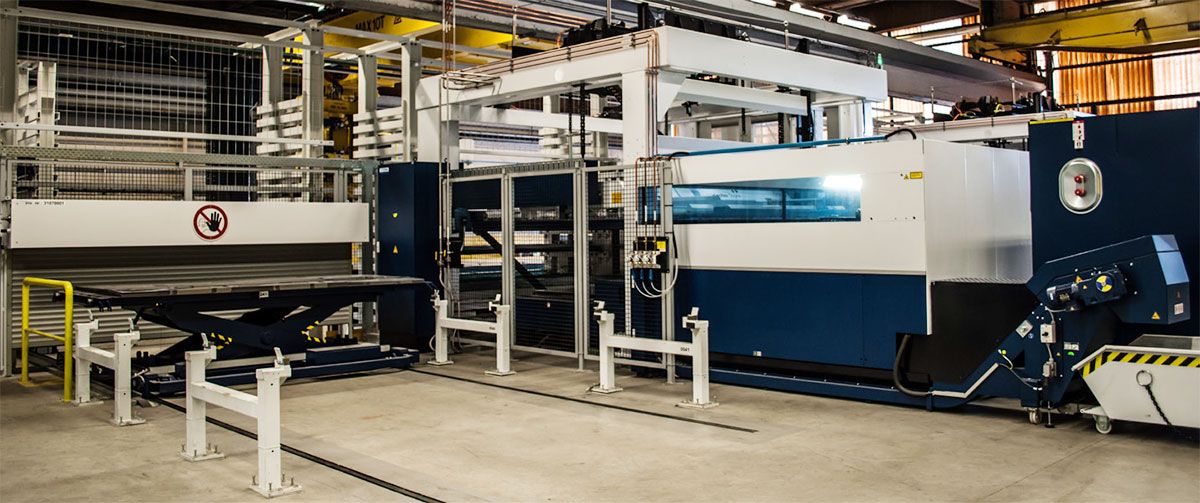
The scissor lift table at the incoming goods station is equipped with storage stamps to hold the sheet metal packages.
Company
CNH Industrial Belgium: Kompetenzzentrum für Erntemaschinen
CNH Industrial Belgium N.V. has been developing solutions for agriculture since 1895. In 2006, the company launched the ‘Clean Energy Leader’ strategy to promote renewable fuels, exhaust gas reduction systems and sustainable agriculture. CNH Industrial Belgium says that through the New Holland brand, it offers arable and livestock farms, contractors, wine-growing operations and professional property maintenance companies the largest selection of user-friendly tractors, harvesters and loaders. The world’s most comprehensive line of agricultural equipment includes more than 80 product lines with over 300 models. It is complemented by efficient parts and customer service, as well as customized financial services. A global dealer network guarantees comprehensive service and expert advice.
CNH Industrial Belgium operates state-of-the-art, globally distributed manufacturing facilities. Four centers of excellence are driving the development of the next generation of agricultural machinery. The Zedelgem plant in Belgium is the center of excellence for harvesting machinery and also a production site. It employs a good 2,800 people. The steel consumption is 157,000 tons per year. CNH Industrial Belgium produces around 3,000 combine harvesters and 375 forage harvesters here every year. In addition, 1,500 square balers are produced for the global market. To do this, 95 types of sheet metal, which vary in terms of quality and thickness, are processed into around 20,000 different parts. Since the end of September 2013, CNH Industrial Belgium has been a subsidiary of CNH Industrie N.V., which was formed from the merger of Fiat Industrial S.p.A. and CNH Global N.V.
A solution on two levels
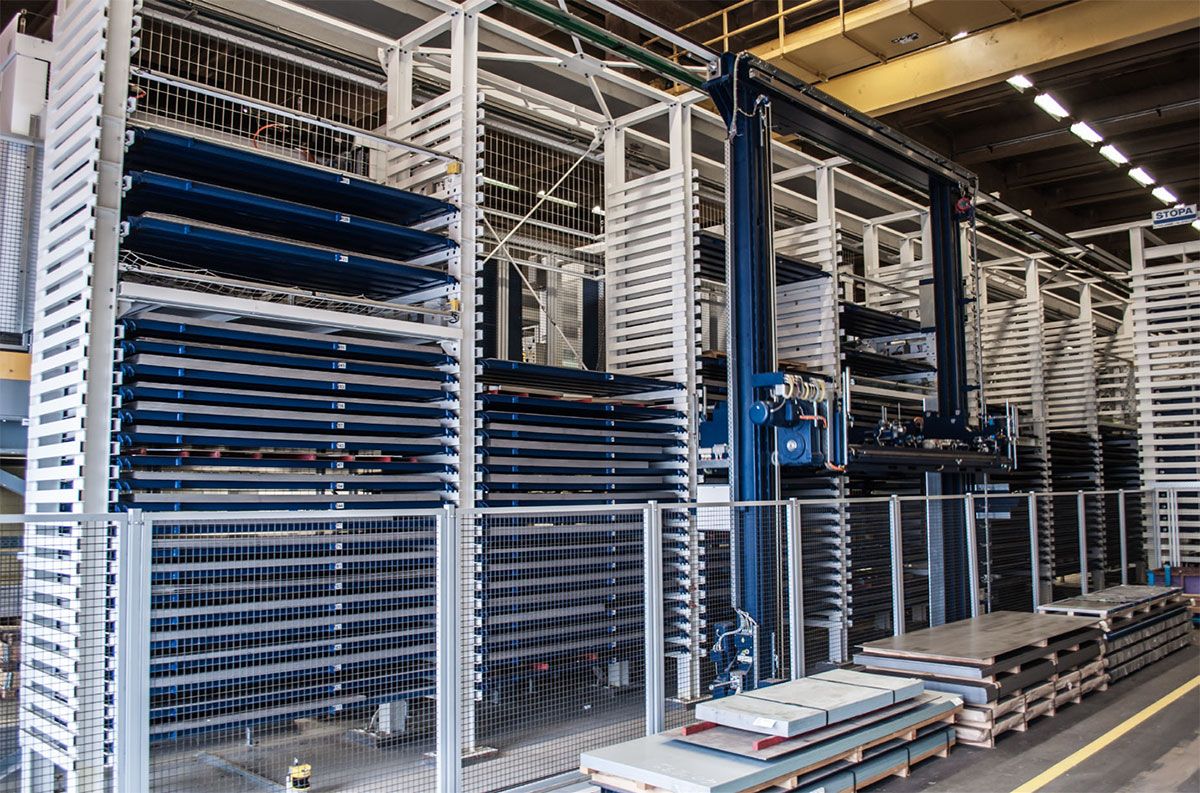
Thanks to the automation, CNH Industrial Belgium has been able to expand its in-house production and has to purchase fewer processing hours from suppliers.
The sheet metal warehouse, which went into operation in April 2013, consists of 18 double-row shelf blocks. It is eight meters high and about 45 meters long and 5.5 meters wide. STOPA has set up the storage compartments for loading heights of 90, 275 and 315 millimeters. The robust double-mast storage and retrieval machine reaches speeds of 150 meters per minute when traveling lengthwise and 23 and 25 meters when lifting and pulling. Thanks to the dynamic (chaotic) storage location management, the flat pallets used, which are designed for payloads of up to 3,000 kilograms, can be stored at random in the free spaces in the rack block. 300 of the pallets used are designed for large, medium and small formats, 15 for maxi, large and medium formats. There are 558 storage locations, 24 of which are reserved for the maxi format.
Johan Vermote climbs the stairs to the 44 x 13 meter concrete platform that has been built in front of the STOPA COMPACT on the second level. “The connection of the four new laser cutting machines on this raised level is a special feature. We needed the level because the space available is limited and we had to install four machines here.” Each of the systems is directly connected to the warehouse by an automatic handling device Lift-Master Store. This means that it is not even necessary to remove the sheets from the system on transport trolleys. The remaining raw sheets, semi-finished products and finished parts are returned to the STOPA COMPACT by the machines.
The system stores the laser-cut components in two stations in the area of three new press brakes that are mounted below the second level. Employees take the parts from the flat pallets, which are located on scissor lift tables, and place them on trolleys or in boxes. They throw the remaining sheets into containers. At these press brakes, as at the laser cutting machines, the operator can produce smaller batch sizes more cost-effectively because more of the work is done inhouse. As a result, stocks of semi-finished parts and the associated capital tie-up are reduced.
Components that are not intended for the press brakes are transported by CNH Industrial Belgium for deep drawing or deep pressing. 70 percent of finished parts go to the welding shop, 20 percent are supplied to other plants and the rest go to the paint shop or directly to assembly.
The system control – consisting of an industrial PC with integrated real-time soft PLC, which is built into an ergonomic control panel – communicates with the TRUMPF TruTops Fab Module Storage via an interface. This software controls the entire material flow of the production and manages all inventories. The cutting orders, nesting and programs are transferred from the work preparation department to the laser cutting machines via the intranet, along with all the information such as sheet thickness and material. The machines then request the sheets from the warehouse and process the orders, while the operators prepare the next ones in parallel to the main time. In addition, the shelf-operating device can use the order data to move pallets with the required sheets to the vicinity of the relevant machines in advance, thus saving time.
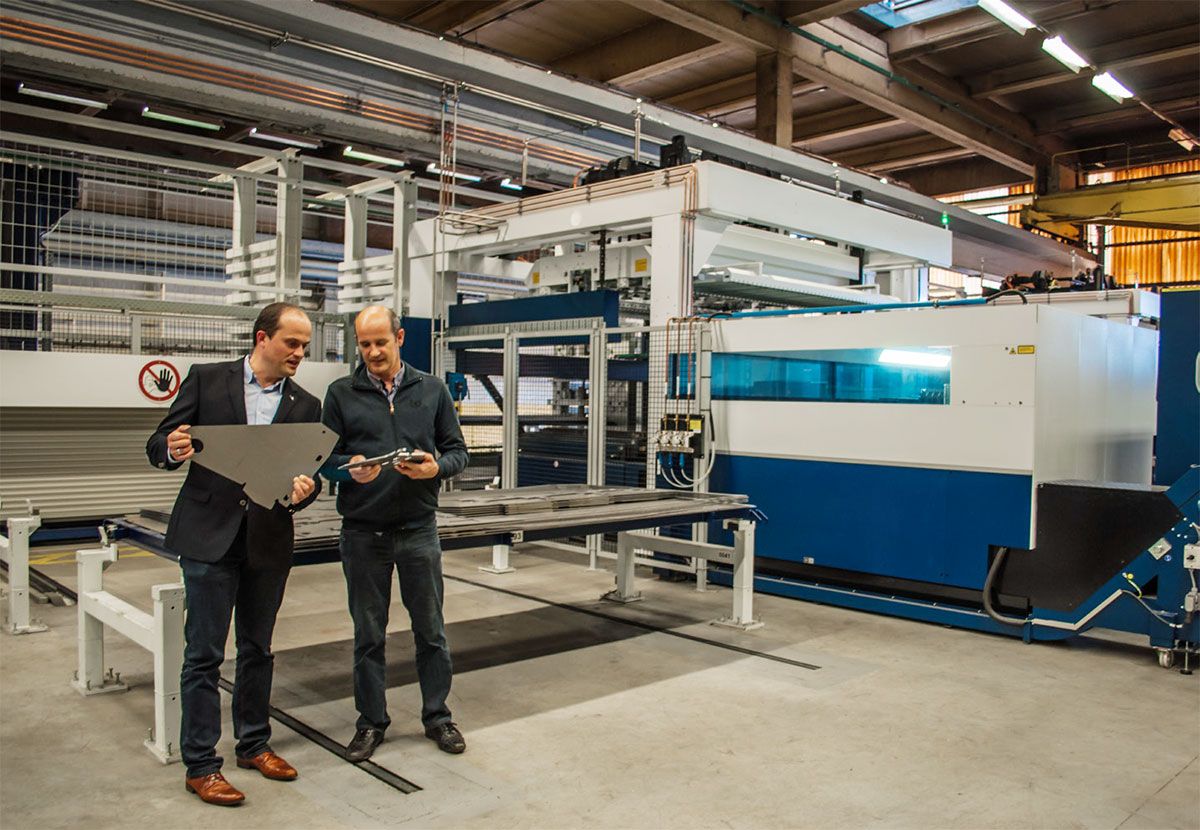
Koen Mergaert, responsible for work preparation, sheet metal processing and turning shop (right), and Johan Vermote, work preparation sheet metal processing at CNH Industrial Belgium.
Author: Jürgen Warmbol
Sales Contact Person
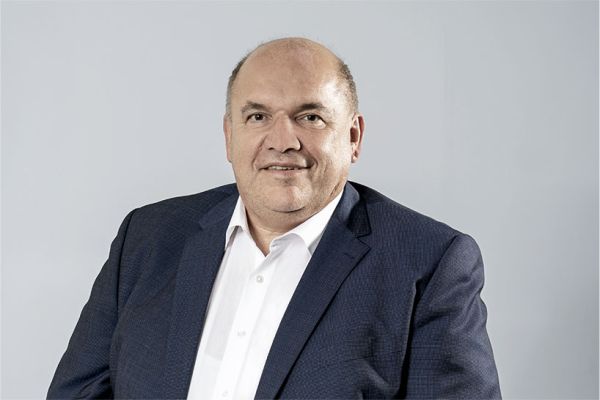
Holger Dehmelt
Sales Engineer Warehouse Technology
STOPA Anlagenbau GmbH
Industriestr. 12
77855 Achern-Gamshurst
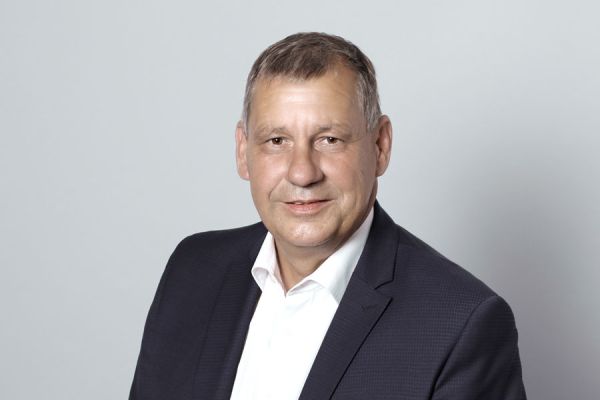
Rolf Eckhardt
Sales Engineer Warehouse Technology
STOPA Anlagenbau GmbH
Industriestr. 12
77855 Achern-Gamshurst
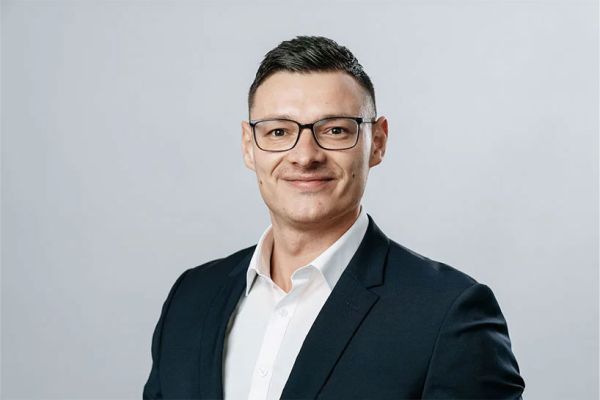
Andreas Pahl
Sales Engineer Warehouse Technology
STOPA Anlagenbau GmbH
Industriestr. 12
77855 Achern-Gamshurst